In most applications, there is a desire to reduce drag. - The strategy for reducing drag depends on whether it is dominated by form drag or skin friction. - Form drag scales with the wake area times the dynamic pressure. - The wake area scales with d squared for a sphere. - The dynamic pressure is 1/2 Rho V squared. - Therefore, the drag coefficient for form drag scales with d squared times R Rho V squared divided by 1/2 Rho V squared times a characteristic area, which is d squared. - If everything is form drag, then the drag coefficient is expected to be of order 1. - On the other hand, skin friction scales with the skin surface area times the wall shear stress. - The skin surface area is d squared and the wall shear stress is tau (which is mu DV by D, with R as the radius). - Therefore, the drag coefficient for skin friction scales with D mu V divided by 1/2 Rho V squared times D squared. - If the drag is predominantly skin friction, the drag coefficient is expected to scale with 1 upon the Reynolds number. - In drag reduction, it is important to note that when the drag is form drag, the wake area can be changed to reduce drag. - When the drag is predominantly skin friction, the skin surface area can be reduced to reduce drag. - Different drag reduction strategies are used for different shaped objects at different Reynolds numbers. - For example, at low Reynolds numbers, a streamline strut has a higher drag coefficient than a circular cylinder due to a larger skin surface area. - However, at high Reynolds numbers, the drag coefficient of a streamline strut is less than that of a cylinder due...
Award-winning PDF software
Video instructions and help with filling out and completing Why Form 8854 Streamlined
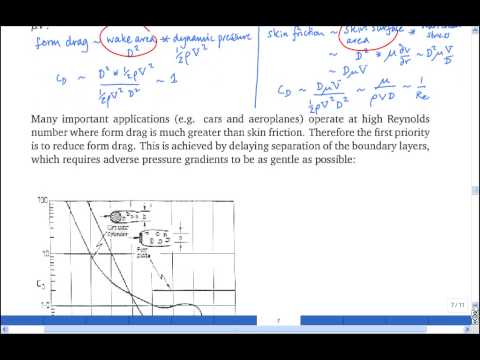